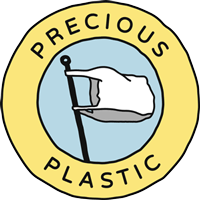
This article is part of Precious Plastic, a One Army project tackling the plastic waste problem. You can learn more
here.
Back in August 2016, I remember opening the first email from Nao (project manager at the UN_HABITAT) and hopping on the, classic, skype call. Many months, tens of emails, meetings and conversations later, in May 2017 we (Dave, Mattia and Emile) finally managed to visit Kenya to set up the first ever Precious Plastic Pilot. A personal victory, as I strongly believed from early in the project in the necessity to test our assumptions and speculations on the ground. And indeed, we’ve learned a great deal from setting up a workspace in a developing country with an extraordinary scarcity of resources, tools and recycling knowledge.
We set up the pilot in Kisii town, a city near Lake Victoria in the North of Kenya. A reality where up to 61% of youths are unemployed and street fires are the norm to get rid of plastic. Perfect circumstances to test Precious Plastic. The project, that will run for the next 12 months, involved three partners- Kisii Government, the UN_HABITAT and , of course, Precious Plastic.
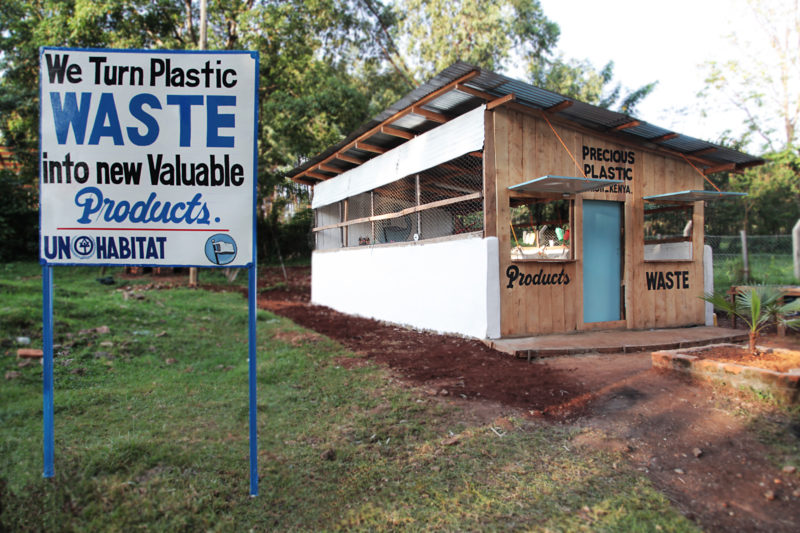
Location Saga
Our original request for a 70 square meters space to create the pilot caused some problems with the Kisii government officials. We were first given a kind of nice building with walls and roof, that made us happy. Then a week before our flights the space became suddenly unavailable and we were offered an old chicken house with crumbling walls, no floor and dripping ceiling. Understanding the possible lack of real estate in an overcrowded city, we got on designing around our new constraints. Until the day we arrived in Kisii and had the first meeting with government officials and ministers (there seems to be a minister for everything 😀), when even the chicken house seemed not to be available any longer. Only after long discussions (where my Italian temperament had to come out 😤) we managed to agree on the chicken house. Hurray 🎉
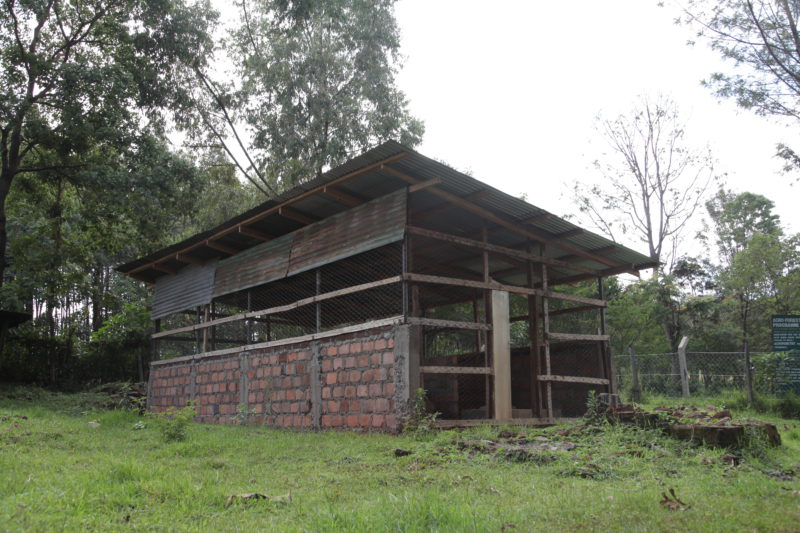
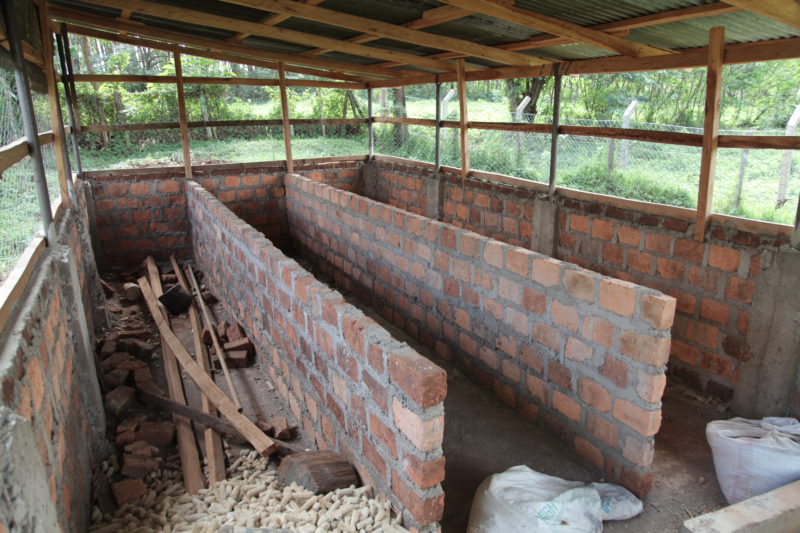
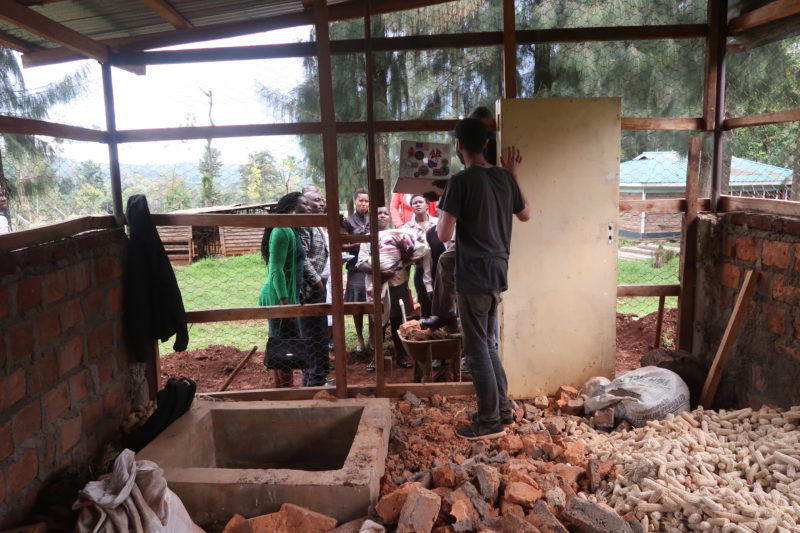
Standards Clash
Finally, we could start building. Or well, demolish. We first had to empty the shed from wobbly walls, storage leftovers and dirt before we were able to even enter the space. Five people from local youth groups helped us all throughout, thanks again guys 👊
.
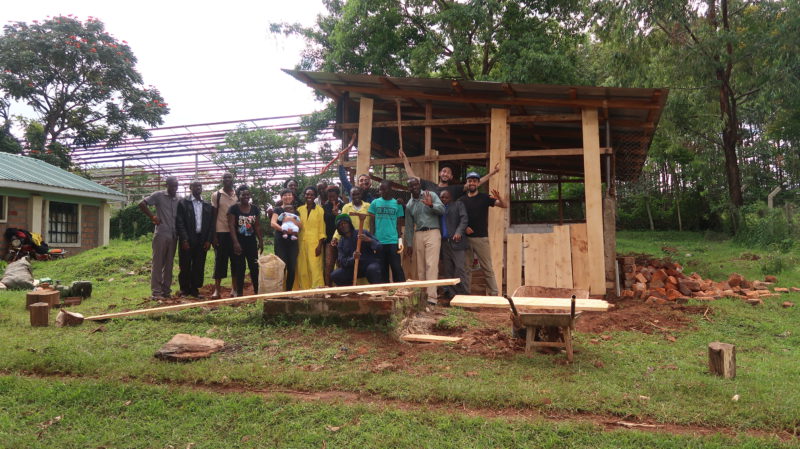
During the first two days of cleaning, washing, sawing, cutting and painting we quickly came to realise the great “standards gap” between our two cultures. A big cultural controversy. What we assume to be common sense, precise work, punctuality, efficiency, attention to detail was nowhere to be found within our Kenyan friend helping us out. It is not to say better or worse, just a completely different set of standards that made the first two days of work particularly stressful. We eventually had to readjust, supervise and take extra care to make sure everything was done somewhere in between our two realities.
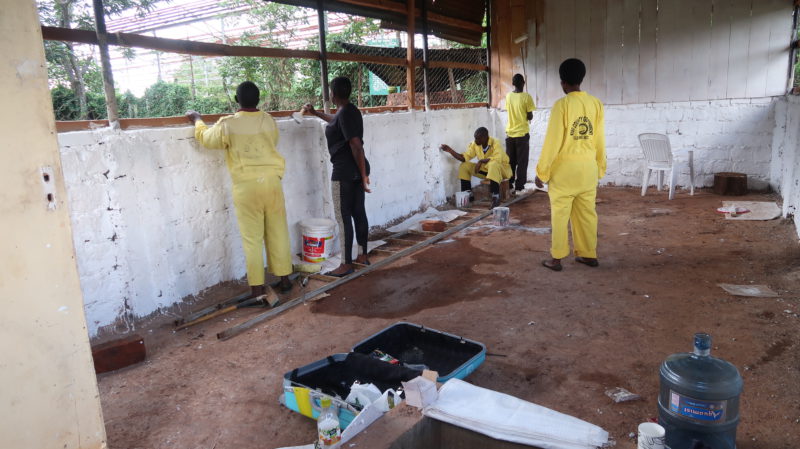
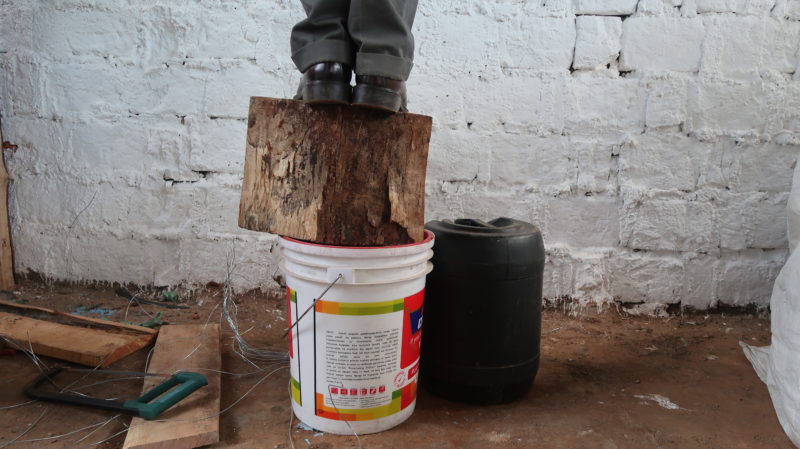
Dear Africa, you are expensive
As a westerner, you think Africa and see poverty, dry landscapes and all the stereotypes connected to the motherland of civilisation. That’s what we’re told from early age through media, education and society. Without much further thinking you assume that Africa must be pretty cheap for our wallets. Whereas this can be true when it comes to food and labour, it is an absolutely false assumption when it comes to sourcing raw materials and components. Metal and wood cost the same or more than in Europe. A second-hand kitchen oven goes four times as expensive as we would buy back home in Holland. Paint and tools are comparable to European prices. Second-hand motors are 8 to 10 times more expensive. Prices are higher and quality is lower. I guess this is the result of neoliberal policies and all the damn Chinese crap that doesn’t make it to our privileged and stricter westerner markets that ends up further polluting Africa. Lack of a proper manufacturing industry adds to the problem.
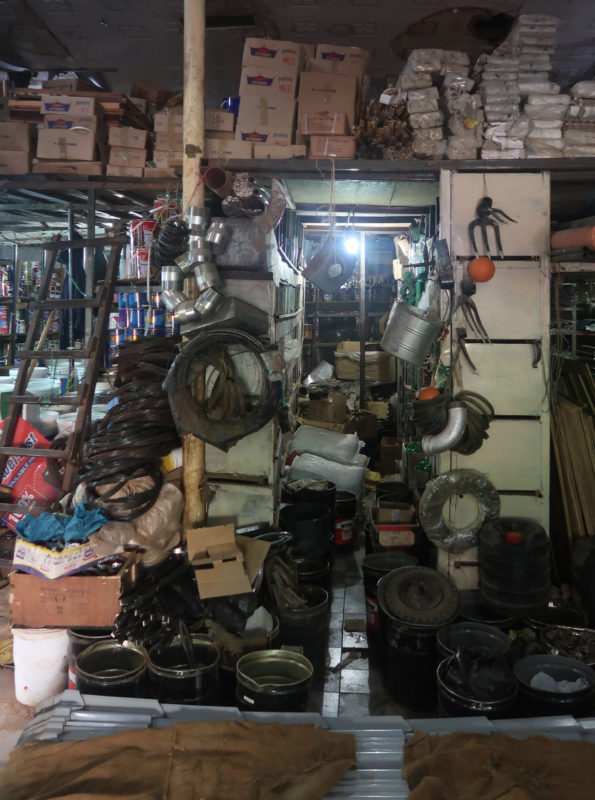
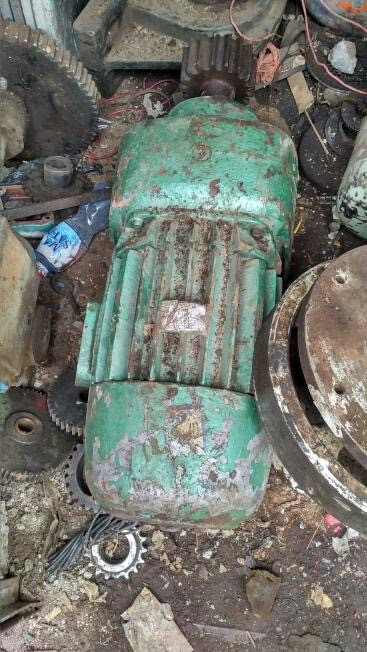
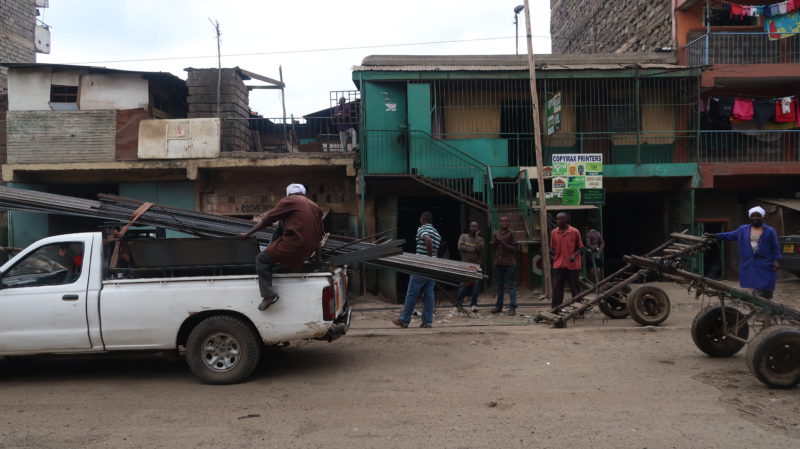
Pole Pole
The generally accepted way of doing things in Kenya is “pole pole”, literally translated to “slowly slowly”. From walking to working, from talking to eating, from nailing to painting, from arriving late to leaving early the accepted norm is “pole pole”. Which is totally fine (they always have time for dancing and laughing for example, which we completely forgot in Europe unless we have a pint in our hands 🍺), but kinda tended to clash with the project’s goal of creating a plastic recycling workspace in little more than a week.
We, westerners on turbo, first hit our heads repeatedly against the”pole pole” attitude around us trying to speed things up, then tried to find workarounds offering incentives but eventually had surrender to the”pole pole” supremacy. We abandoned punctuality, adjusted to early leaves, accepted long queues at checkouts and pushed even harder on ourselves to get things ready on time.
Source locally
Precious Plastic is built upon the local availability of materials and components so that everyone can make the machines everywhere in the world and start recycling. For the Kenya pilot, we tried to source as much as possible locally, in line with our philosophy. However, reflecting on the experience we came to realize that maybe, this wasn’t the best decision. We are not sure whether for future pilots we should source locally or bring components and parts directly from the Netherlands. Let me explain, taking the motors as an example.
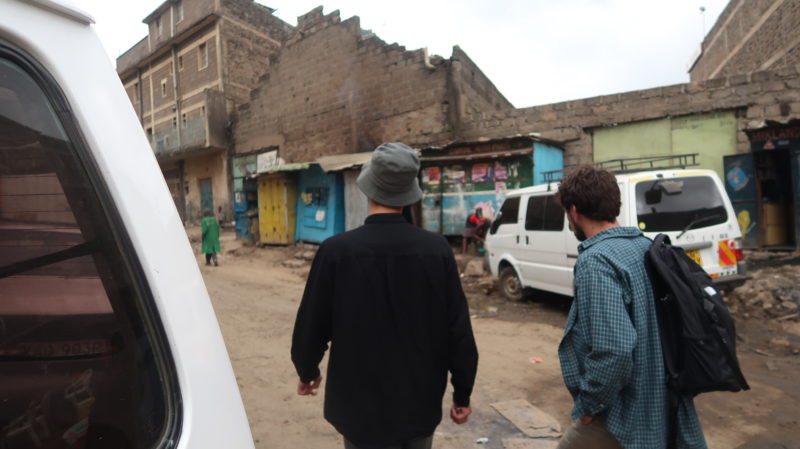
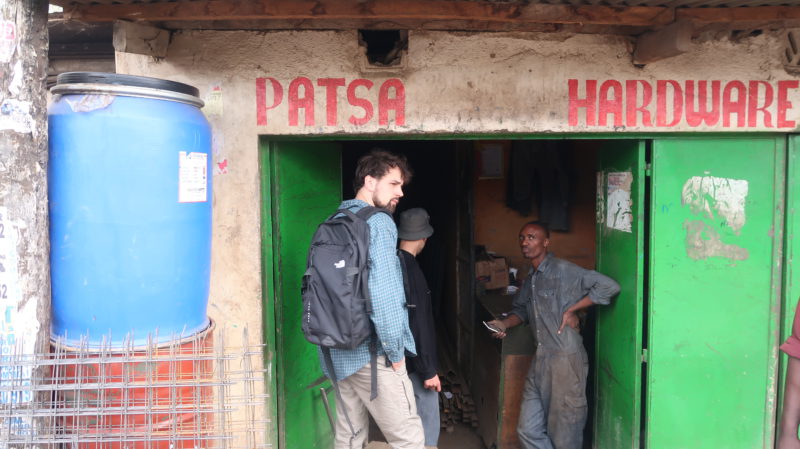
Buying the motors locally was a huge headache- logistic, quality control, price, warranty and transport was a tough experience. Being 10.000km away made it difficult to get a feeling of the quality, RPM, state of the motor and other qualities that are key to chose the best possible (secondhand) motors (we ended up buying a motor that must have been 80kg 😱). From a sustainability perspective also doesn’t make much sense, only pushing the CO2 baggage of the delivery a few years back since all motors in Kenya were either European made (Italian or German) or shitty Chinese quality. The motors were already imported, so next time we might as well deliver them ourselves saving on headaches and improving the quality of the machines we can deliver.
What’s your thoughts on this? We would love to know what the community thinks in regards.
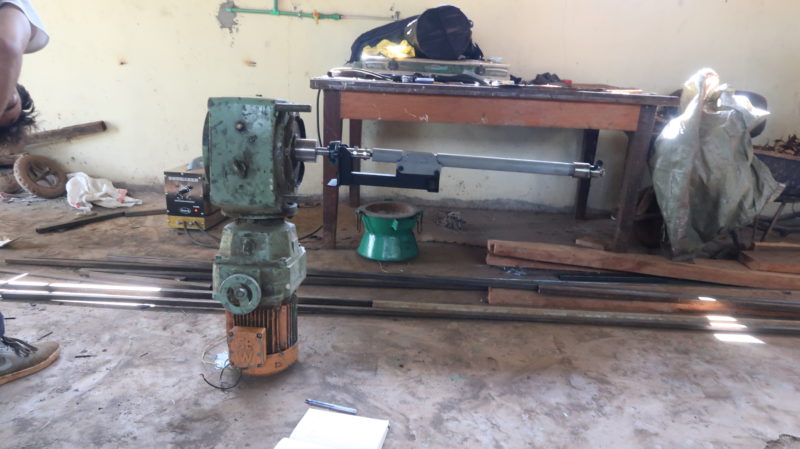
Welding machine
To put together the machines we were given a welding machine from a local handyman. Happy to even have found one, we quickly got on with stick welding (Dave was crying for his TIG back home 😭). After a few days of struggles with weak welds, a slow & tiring process, weld eyes and splinters in Emile’s eye we found ourselves (three days from opening) with two machines still to build and the realization that all welds we made till then had to be redone due to the poor quality of the machines and weld sticks (shitty Chinese crap).
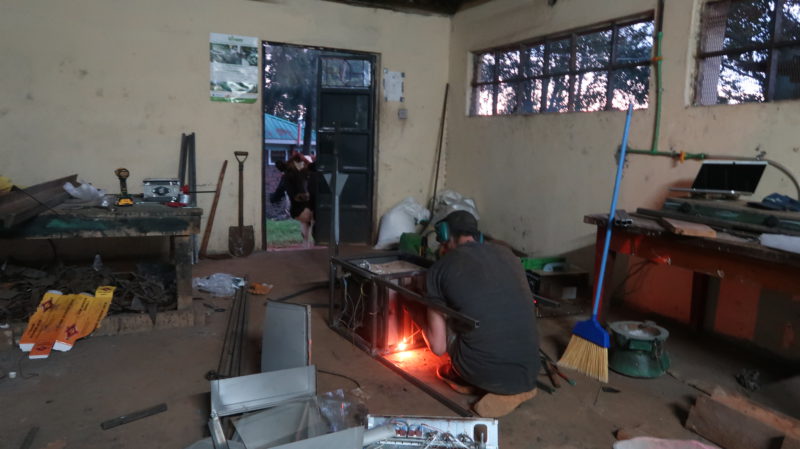
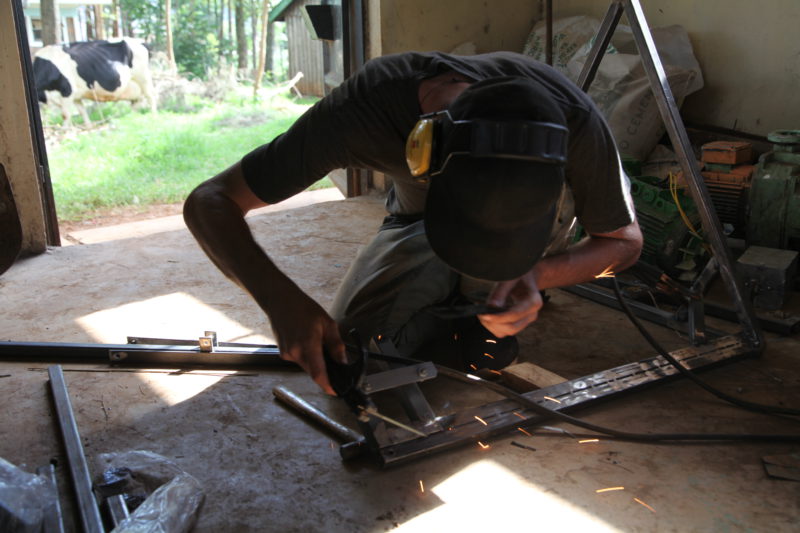
And that’s when Ken (yhe, this Ken) came in our help with his time travel (23 years old) welding machine. He nailed it. And two days later we had the four machines ready, strong and solid. The three of us were absolutely in love with Ken’s machine and its long history of repairs, problems, fixes and maintenance. It is incredible how you can bring a tool to its max. Spoiled European throwing away stuff first time they stop working 😡
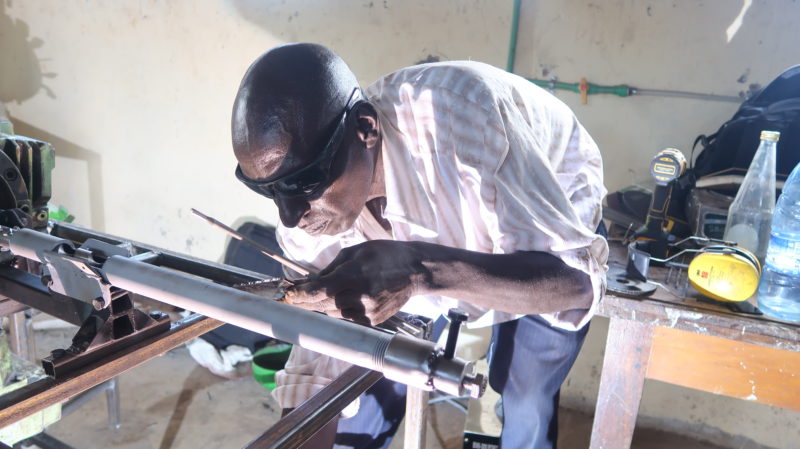
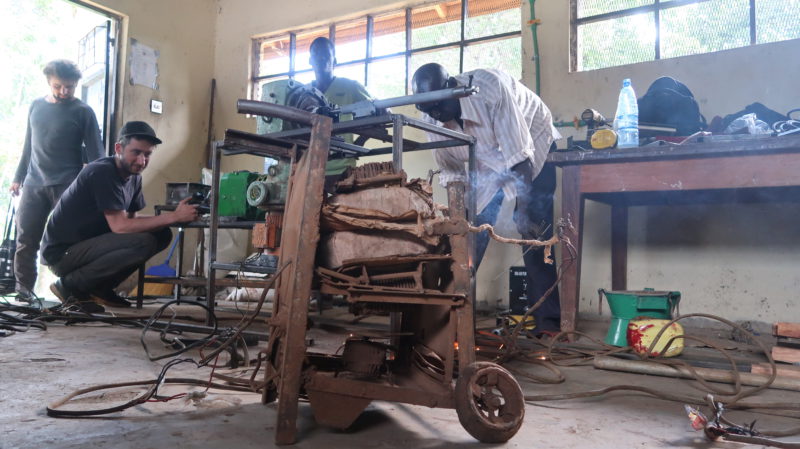
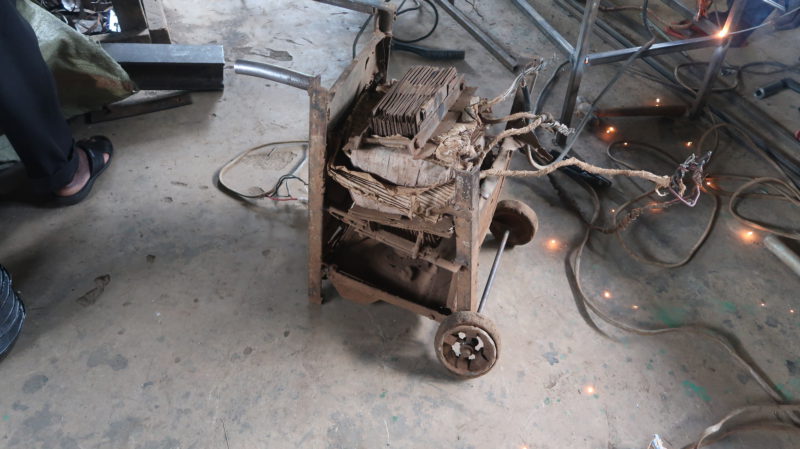
Conclusions
It was though. To transform the chicken house in a plastic recycling workspace with a full set of machines in 10 days was indeed a great challenge. On a tight deadline. By the end we were pretty tired (destroyed)
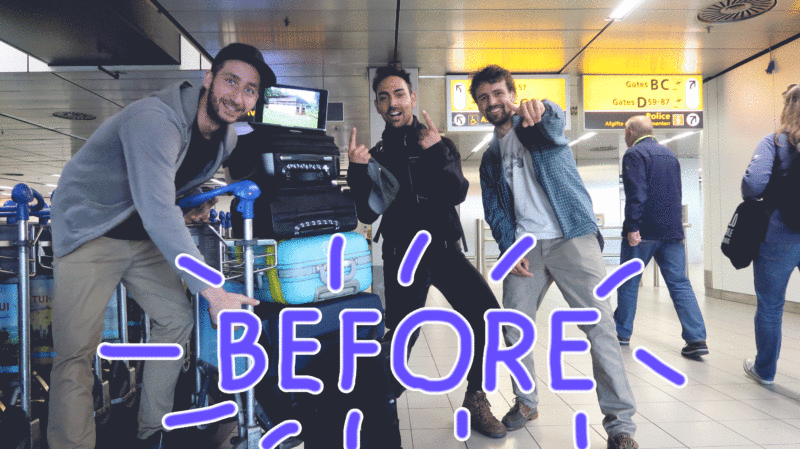
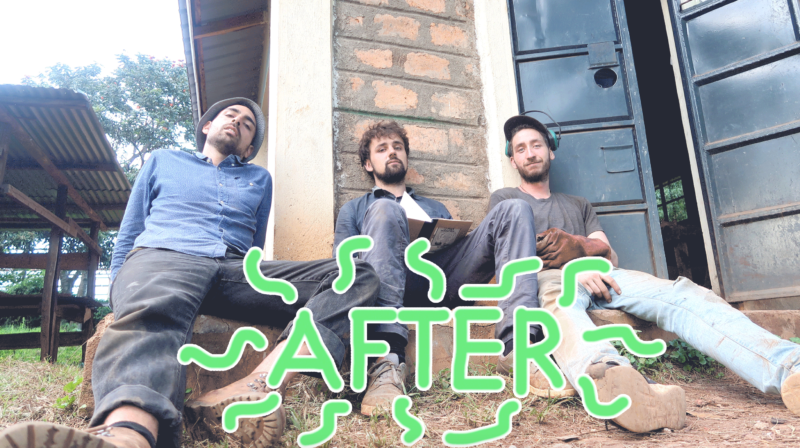
But we truly enjoyed the experience and learnt a lot about setting up Precious Plastic in developing countries. And people in Kisii are now recycling plastic daily- you can follow their updates on facebook. Here is a few pics we took of the workspace and training.
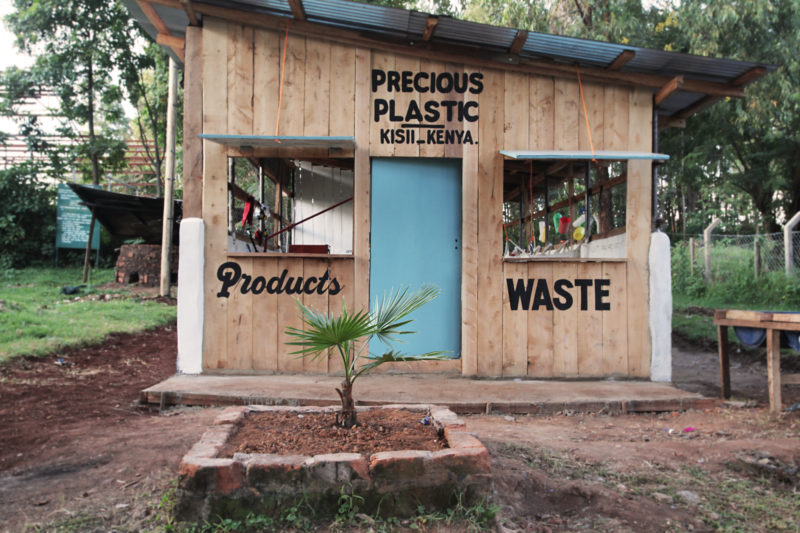
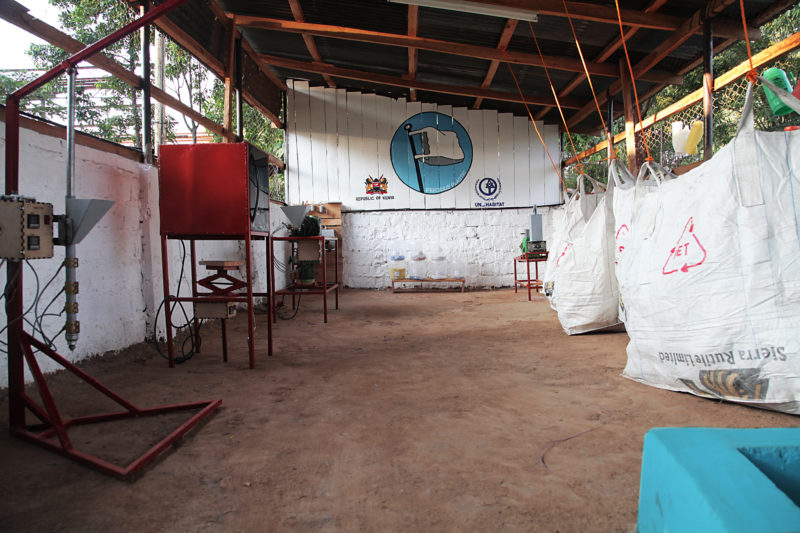
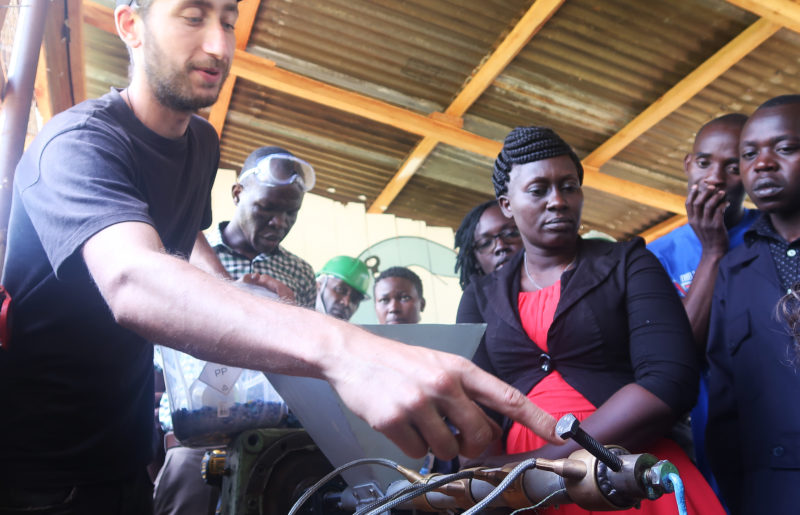
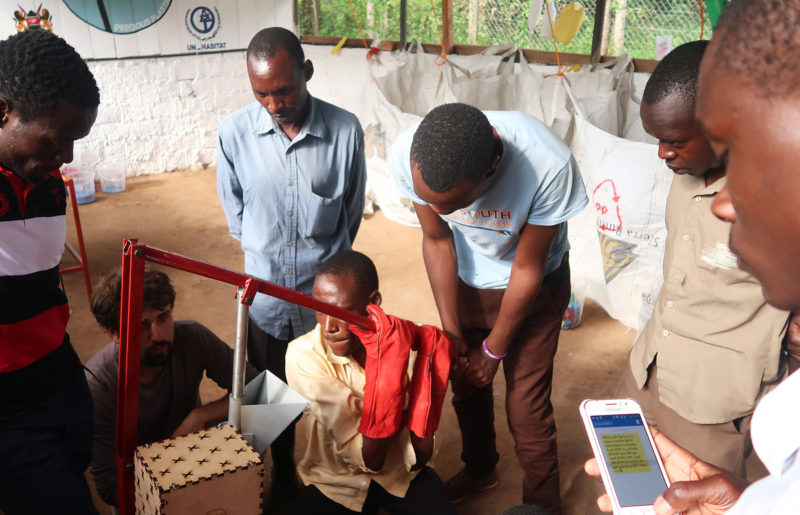
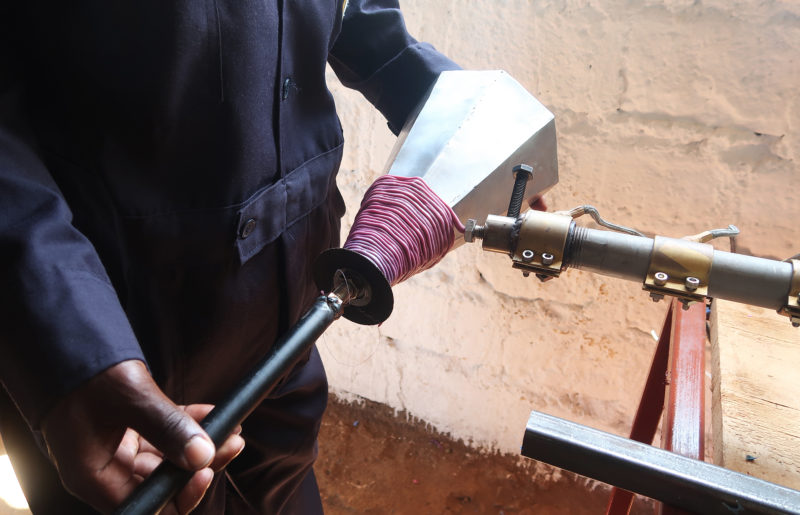
We had an incredible time in Kenya, with insane juices, too many candy bananas, plenty of Ugali, lots of laughs and fun dances with fellow builders, politicians and glue kids in the streets. The learning experience has been very beneficial and constructive with a lot of material to reflect on. All we’ve learned will be soon opensourced with our community to help the process of setting up a Precious Plastic workspace everywhere in the world. Stay tuned!
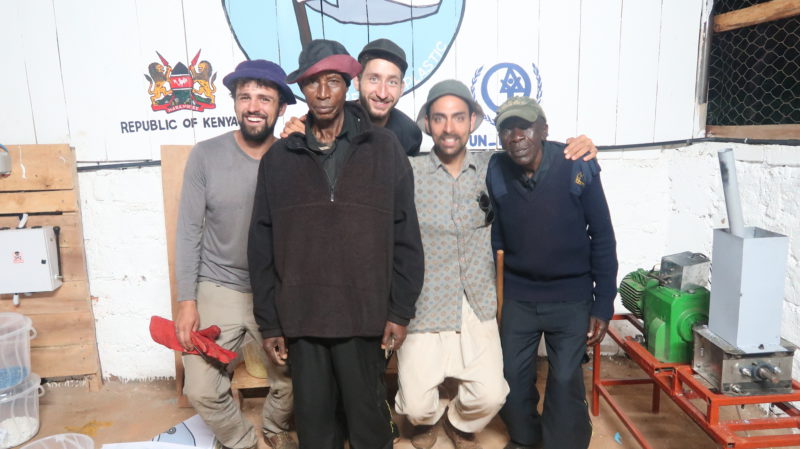
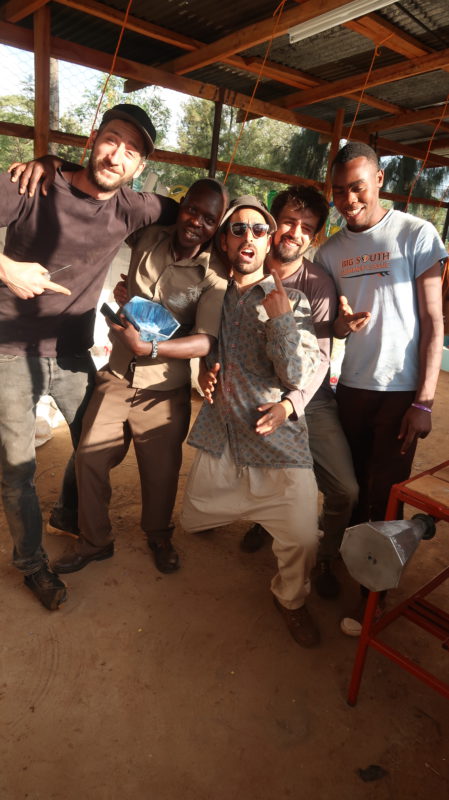
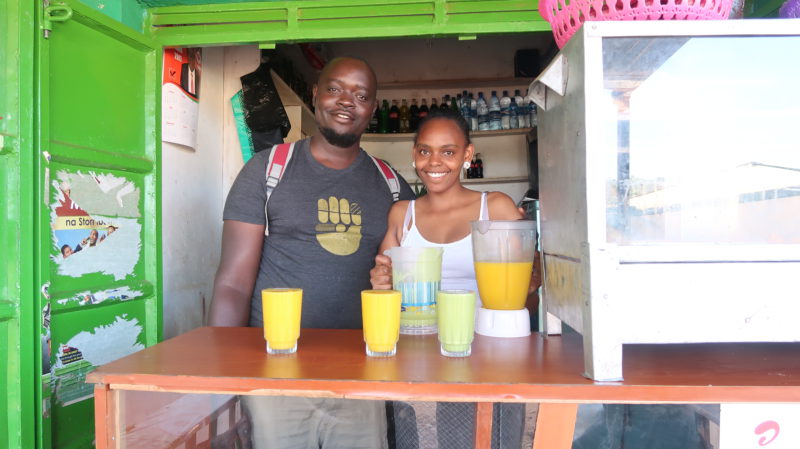
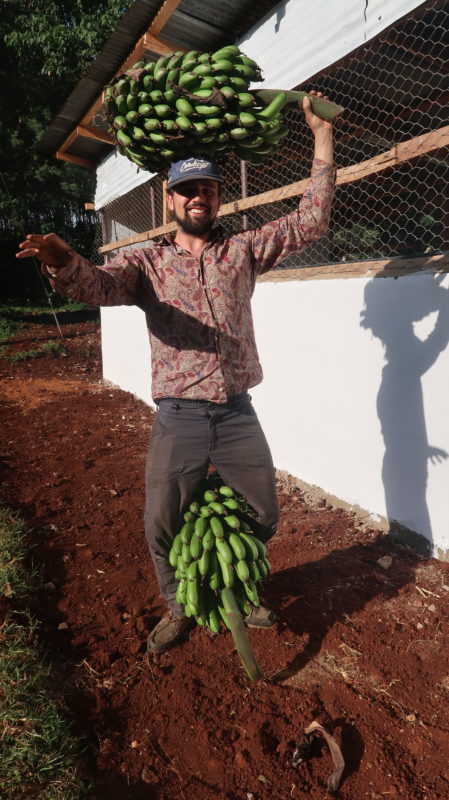